Business
Conveyor Belt Systems: 6 Ways to Improve Efficiency
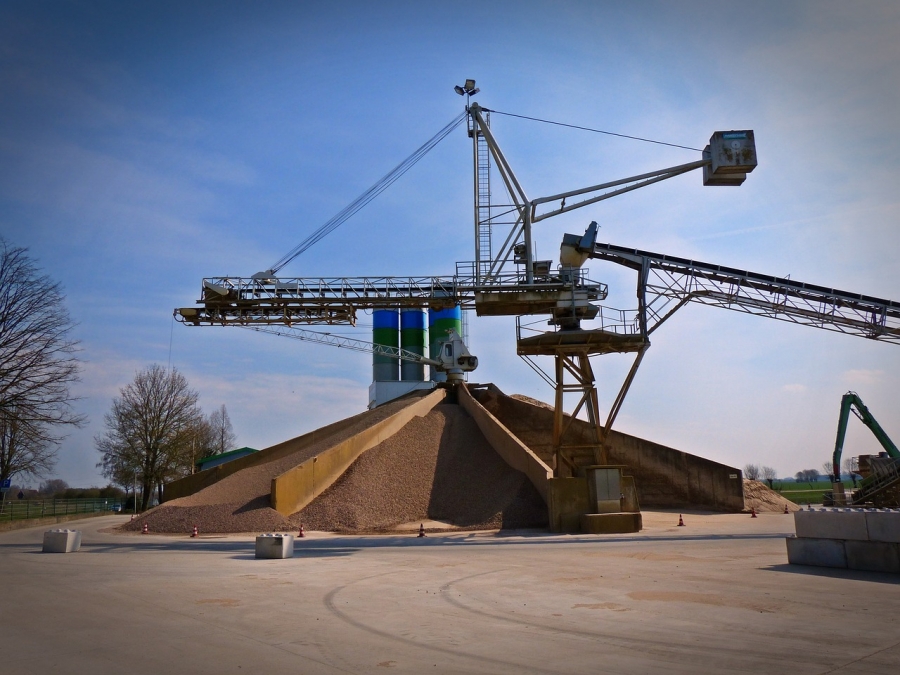
You might think that conveyor belt systems cannot be improved because of the simplicity of their design. After all, how do you make a system that runs 24/7 more efficient? Well, there are at least 6 ways to do so, from inspecting the loads the conveyor transports to fostering a culture of safety.
1. The structure of the load
From the sheer size of the load the belt has to carry to its dimensions and weight, you should take care not to overload the conveyor. Most industrial conveyors won’t stop or break when you overload them but their efficiency rate will plummet.
Based on its structure (belt material, driveshaft, motor, etc.), every conveyor model has certain specifications regarding the load it can bear. Always try to stay within the manufacturer’s specifications if you wish the conveyor to run efficiently.
2. Inspect the conveyor often
There are some conveyor models that can run longer than a human can live! However, the secret to any conveyor’s longevity is proper maintenance. Inspect the conveyor at regular intervals to make sure all parts, from the pull stop to the railings are functioning without a hitch.
Another purpose of these inspections is to be able to calibrate the machine. This is important both for the operator, as well as for meeting the industry standards. A belt can easily get out of alignment after vibrations, human contact, or when a handcart bumps into it by accident.
3. Clean the belt regularly
Apart from making sure that all conveyor parts are fully operational, the belt should be as clean as possible. In factories and warehouses, spillages are a common occurrence but operators and business owners tend to overlook a dirty belt.
However, if oil spills on the belt, it can shift it and even cause it to slip off completely. That’s why you need to use a conveyor belt cleaner every time there is a spill. By doing so, you ensure the conveyor is safe to operate, thus increasing its efficiency in the long run.
4. Pushing versus pulling
Modern conveyors come with several modes, including the selection of whether you want the conveyor to push or pull. The latter is a far more economic option, as research suggests that a convey belt loses half of its load-bearing capacity when pushing.
Although conveyors have the “push” option, pulling has more sense in terms of productivity.
5. Watch the flow rate
In the mining industry, the maximum load of a conveyor system is more important than its speed. On the other side, speed matters in conveyors found at airport terminals, while the load-bearing capacity is secondary.
Depending on the environment a conveyor operates is the flow rate is going to matter more or less. For airports and distribution centres, a fast-moving conveyor is a must. Also, make sure you have the specific equipment necessary to load and unload certain types of conveyors.
6. Safety first!
It might seem odd but by increasing safety, you are actually increasing the efficiency of the average conveyor system. Namely, every time an accident occurs, regardless of how minor it may be (a malfunction or an injury), the conveyor grinds to a halt.
Since conveyor systems are designed to operate around the clock, every second they spend motionless is a financial loss for the owners. That’s why it pays off to nurture a culture of safety that stimulates workers to report possible security issues right away.
As you have seen from our 6 examples, the efficiency of a conveyor belt can be increased. Every day that goes by without an injury or a malfunction is considered a success, as you have managed to keep the conveyor running.
-
Tech10 years ago
Creating An e-Commerce Website
-
Tech10 years ago
Design Template Guidelines For Mobile Apps
-
Business5 years ago
What Is AdsSupply? A Comprehensive Review
-
Business10 years ago
The Key Types Of Brochure Printing Services
-
Tech8 years ago
When To Send Your Bulk Messages?
-
Law4 years ago
How Can A Divorce Lawyer Help You Get Through Divorce?
-
Tech5 years ago
5 Link Building Strategies You Can Apply For Local SEO
-
Home Improvement5 years ago
Hоw tо Kеер Antѕ Out оf Yоur Kitсhеn