Laser cutting is a process that involves a technology for cutting precisely a material with a high-powered laser beam. A computer (CNC – Computer Numerically Controlled) is used for directing a laser along coordinates onto the object which is going to be cut. Laser cutting is being used for many purposes, among which one is to cut metal plates.
Laser cutting techniques are typically very expensive and highly sophisticated, which are controlled by computers. Therefore, they are being used mostly in industries rather than in a DIY environment.
When talking about metal laser cutting services, it is considered to be the most accurate method, allowing the freedom to cut every shape or hole. Moreover, it makes a very clean cut while maintaining a magnificent cut quality as it has a very small HAZ (Heat Affected Zone) along with a small kerf width.
How Does Laser Cutting Work?
Varieties of the laser are used for cutting materials of different types. Though all the things involved in the technique are different, the basic principle of working are the same. The energy is converted into a high density beam of laser light that is highly focused.
The laser beam is a column that includes a single wavelength, color or high-intensity light. While working with a typical CO2 laser, the wavelength is kept in the part of the light spectrum of Infra-Red. This is done for keeping it invisible to the human eye.
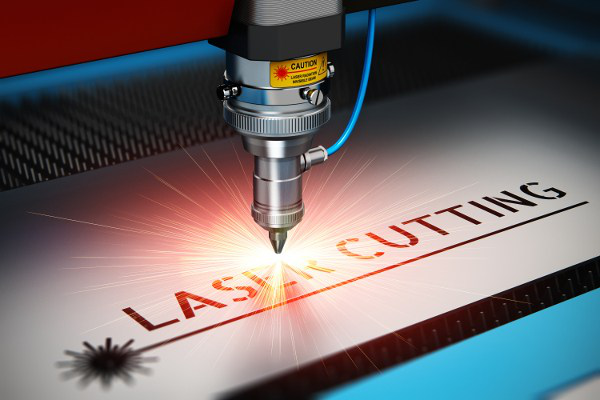
The laser beam is only about 1 – 2 mm in diameter. This low flow is kept as it travels through the long path of the machine. Although the diameter is so small, the laser beam is powerful enough to either melt, burn or vaporize on the application whichever material comes in its path. In case, a mirror comes in between, it may bounce in different directions. This happens even before the beam hits the metal plate which termed as “beam benders.”
In the case of non-bouncing, the laser is directly focused through the bore of a nozzle for hitting on the plate. Additionally, the compressed gases such as Oxygen or Nitrogen is present in the bore when it passes through the nozzle.
When it comes to focusing of the laser beam, it can be done either through a curved mirror or special lens. It is performed in the laser cutting head. For getting desired shape and cut, the beam has to be precisely focused. It ensures that the density of energy and beam is directed perfectly in the shape of a circle to burn the spot. This insures that consistency and precise measurements both are maintained.
As the laser metal cutting service includes high power density, it yields rapid heating, melting, and vaporizing (Partially/Completely) of the metal. The heat of laser beam is kept normal as the oxy-fuel burning process requires for cutting mild steel. In the same way, the laser cutting gas will be pure oxygen, as it requires for the oxy-fuel torch. This way it simply melts the material, while keeping the pressure of nitrogen high enough to blow out the molten metal.
If a CNC machine is used for laser metal cutting services, it is moved over the material. It moves in such a way that it brings out the desired shape. The height between the nozzle and the metal plate is maintained by using a capacitive height control system. Maintaining this distance becomes important as it ensures that the focal point is relative to the surface of the metal. If the focal point of the surface plate is raised or lowered a bit, the cut quality can affected.
Conclusion
While there are many other uses of the laser, the cutting technique is one of the most popular ones. Due to this reason, laser metal cutting has expanded over recent years. However, the quality and precision of laser cutting depends on the operator, especially for sheet metal fabrication. The better the technician, the better is the output. Therefore, considering a reliable and experienced supplier such as Metalscut4u.com can make a great difference for getting precision.